What Are the Manufacturing Processes for the Pre-treatment of Knitted Fabrics?
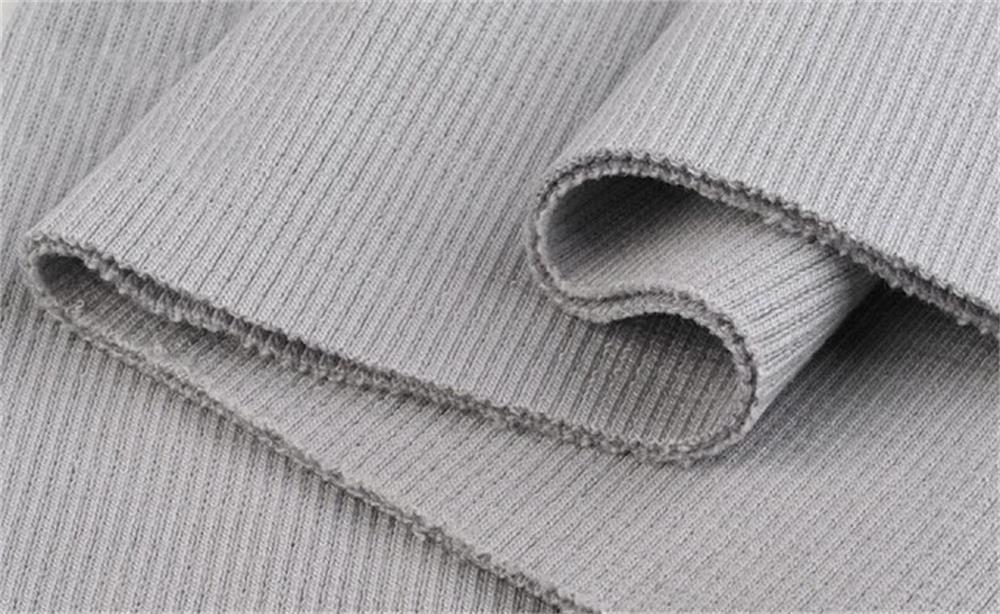
The knitted fabric has a soft feel, good breathability, elasticity, and comfortable wearing. It is often used to make singlets, cotton sweaters, sweatshirts, gloves, and socks. Knitted fabrics are composed of loops, so the structure is loose, it is easy to deform under the action of external force, and cannot withstand greater tension.
Therefore, the fabric must be kept in a relaxed state during processing, and low-tension processing equipment should be used. At the same time, the processing process should be shortened as much as possible. QIKUN TEXTILE shared the following pre-treatment processes for different knitted fabrics.
Pre-treatment of cotton knitted fabric
The main products of cotton knitted fabrics are jerseys, cotton wool cloth, and so on. The knitting yarn is not sizing before weaving, so there is no sizing on the fabric. In the pre-treatment process, singeing and desizing are generally not carried out, and usually only scouring, bleaching, and softening are carried out. Some varieties (such as jerseys) also need alkali shrinkage to increase the density and elasticity of the fabric. The pretreatment process of cotton knitted fabrics mainly has the following forms.
Bleaching jersey process: grey cloth→alkali shrinkage→scouring→sodium hypochlorite bleaching→hydrogen peroxide bleaching→whitening→softening treatment→dehydration→drying
Dyeing single jersey process: grey cloth→alkali shrinkage→scouring→sodium hypochlorite bleaching→dyeing (printing)→finishing
Dyeing cotton wool cloth technological process: grey cloth→scouring→sodium hypochlorite bleaching→dyeing (printing)→finishing
1. Alkaline shrinkage
Alkali shrinkage is a process in which cotton knitted fabrics are treated with a concentrated alkali solution in a relaxed state.
(1) The purpose and steps of alkali shrinkage The purpose of alkali shrinkage is mainly to increase the density and elasticity of the fabric, improve the strength of the fabric and improve the gloss, and reduce the shrinkage rate of the fabric. The completion of the alkali shrinkage process involves three steps: padding alkali solution, stacking shrinkage, and washing to remove alkali.
(2) Equipment for alkali shrinkage of knitted fabrics. Cylindrical knitted fabric alkali shrinkage machine is a combined machine composed of cloth feeding board and soaking tank, rolling car, alkali washing tank, cloth storage tank, and cloth doffing device.
(3)Alkali shrinkage process. Alkali shrinkage process conditions: caustic soda 140-200g/L, room temperature, time 10-20min. The process flow of alkali shrinkage: sewing head→expansion→padding thick lye→stacking (or dipping in concentrated lye)→dealkalizing→hot water washing→cold washing of knitted jersey dry shrinkage) and wet cloth alkali shrinkage (wet shrinkage).
Dry shrinkage is the alkali shrinkage of knitted grey fabrics and then scouring. Wet shrinkage means that the knitted grey fabrics are scoured first and then alkali shrinkage. The former has a simple process, but the fabric absorbs alkali unevenly; The latter has uniform alkali absorption, good elasticity, and gloss, but the process flow is longer, and dry cloth alkali shrinkage is often used in actual production.
2. Scouring
(1) The purpose of knitting fabric scouring is to remove the cottonseed hulls, the viscose symbiosis on the grey fabric, and the oily impurities stained during weaving. Knitted fabrics can be boiled in a cloth pot and rope steaming. No matter which method is used, the scouring conditions should be milder than that of ordinary cotton cloth. The purpose is to keep the more baked matter on the cloth, so as not to affect the feel of the fabric and cause sewing holes.
(2) The scouring process The continuous steaming and scouring process of knitted fabrics is as follows: knitted fabric after alkali shrinkage→padding scouring liquid→steaming→60-70℃ hot water washing→cold water washing→pickling→cold water washing →neutralization→cold water wash
3. Bleaching
Sodium hypochlorite, hydrogen peroxide, and sodium chlorite can be used as a bleaching agents for knitted fabric bleaching.
(1) Sodium hypochlorite has a general bleaching effect, easily damages fibers, and has a greater impact on the environment, but its cost is low and the equipment is simple. Therefore, it is still widely used in bleaching cotton knitted fabrics, and it has been gradually replaced by hydrogen peroxide.
(2) Hydrogen peroxide has a good bleaching effect, little damage to fibers, and a certain degree of impurity removal. It is not only suitable for cotton, but also enables other fibers to obtain good bleaching effects, so it is especially suitable for bleaching cotton and synthetic fiber blended fabrics.
(3) Sodium chlorite not only has a good bleaching effect but also has little damage to the fiber and has a strong ability to remove impurities. It has wide adaptability to fibers and is an ideal bleaching agent. However, its cost is high, it is corrosive to equipment, and emits toxic gas during bleaching, which has a greater impact on the environment, so its use is greatly restricted. The process and conditions of bleaching knitted fabrics are similar to those of ordinary cotton fabrics. For products with high whiteness requirements, re-bleaching and fluorescent whitening are also required.
4. Soft treatment
In order to prevent sewing holes in knitted fabrics when they are made into garments, in addition to taking appropriate measures during scouring, softening treatment is also required. The softeners often used in knitted fabrics are mostly homemade paraffin wax emulsions, so the softening treatment is also called waxing. For ease of use, softeners are sometimes used.
Pre-treatment of polyester knitted fabric
The purpose of the pre-treatment of polyester knitted fabric is to remove the oil and antistatic agent applied to the fiber during spinning and the oil stains on the weaving. All fabrics that are set before dyeing must be pre-treated to avoid defects caused by oil stains and impurities on the fibers during heat setting.
For the pretreatment of polyester knitted fabric, 0.5%~1% (weight of the fabric) soap or synthetic detergent solution can be added to a small amount of soda ash, treated at 80~90℃ for about 30min, and then washed in hot or cold water.
Pure polyester knitted fabric does not need to be bleached, because polyester itself is already very white, even if it is an extra-white variety, it can reach the whiteness requirement by only performing fluorescent whitening.
Pre-treatment of medium-length chemical fiber fabric
Medium-length chemical fiber fabrics are mainly polyester viscose fabrics, and there are polyester-acrylic blended medium-long fiber fabrics and polyester-acrylic viscose blended medium-long fiber fabrics. Medium-length chemical fiber fabrics are all wool-like fabrics. Thick fabrics require full hand feel, fluffy, good elasticity, and a thick wool style. The pros and cons of these styles depend on the quality of dyeing and finishing.
The medium-length chemical fiber fabric does not contain natural impurities, and the scouring and bleaching process is relatively simple, requiring only singeing, resizing, and heat setting. The pretreatment of medium-length chemical fiber fabrics must adopt a loose processing technology to improve the wool-like effect.
1. Singeing
The singeing process with less flame, strong flame, and fast speed is adopted. The arrangement sequence of the singeing process can be determined according to the factory conditions and various requirements. For varieties that are dyed with high temperature and high pressure, the singeing should be carried out after dyeing, so as not to affect the uniformity of dyeing.
2. Desizing
Desizing is carried out in loose, damp, and heat processing so that the fabric can fully shrink while desizing, so as to obtain a fluffy and plump wool-like style. PVA on medium-length chemical fiber fabrics is the main size, and alkali desizing or oxidizing agent desizing can be used.
After alkali desizing, the fabric feels a little harder and dyed in the same hot-melt condition to give a slightly darker color. Desizing can also be done with detergent. The fabric after desizing has a soft hand, good elasticity, and easy tentering. After desizing and washing, it is washed again on the loose-type washing machine and then dried on the loose-type dryer.
3. Heat setting
The appropriate setting temperature is 190℃. Shaping before dyeing can ensure dimensional stability during the dyeing process, reduce wrinkles, and improve dyeing quality.
The knitted fabric designed and manufactured by QIKUN TEXTILE has a strong structure, is suitable for a variety of cutting methods, and can be widely used in the clothing manufacturing industry. If you want to know more about knitted fabrics after reading the above, you can get a comprehensive solution by contacting us.
As an experienced fleece fabric manufacturer, we have accumulated rich experience in this field. Regardless of product selection or production, we have carried out strict quality control. We also prioritize customer needs and provide customers with a variety of options and sufficient inventory. If you want to buy our fleece fabric, please do not hesitate to contact us immediately!